In the steel fabrication industry, the decision to use welding robots or manual welders can significantly impact production efficiency, quality, and cost. Both options offer unique advantages and drawbacks, and the choice largely depends on the specific needs of a business. This article examines the pros and cons of welding/assembly robots versus manual welders, helping businesses make an informed decision.
Before starting, it’s necessary to point out the difference between an assembly robot, which refers to fitting operation, and a welding robot, which carries out welds on already fitted parts.
Assembly/Welding Robots: Pros and Cons
Assembly/Welding robots are highly efficient tools designed to automate fitting and welding processes, typically in high-volume production settings. They offer significant productivity boosts, operating 24/7 without the need for breaks or rest. This constant output increases throughput and reduces production time. Additionally, robots ensure high precision and consistency, producing uniform welds across large batches with minimal variation. This level of precision is crucial in steel fabrication, where quality control is vital.
However, the initial investment in welding robots is considerable, even if those amounts have drastically reduced over the past couple of years. The cost of purchasing, installing, and programming the robots can be a significant barrier, especially for small businesses. Once set up, robots do excel at repetitive tasks, but they lack flexibility when it comes to handling complex or custom jobs. Reprogramming robots for different tasks can be time-consuming and costly, making them less efficient for smaller production runs or unique projects. Maintenance is another challenge, as robots require regular servicing to prevent breakdowns, which could lead to production downtime.
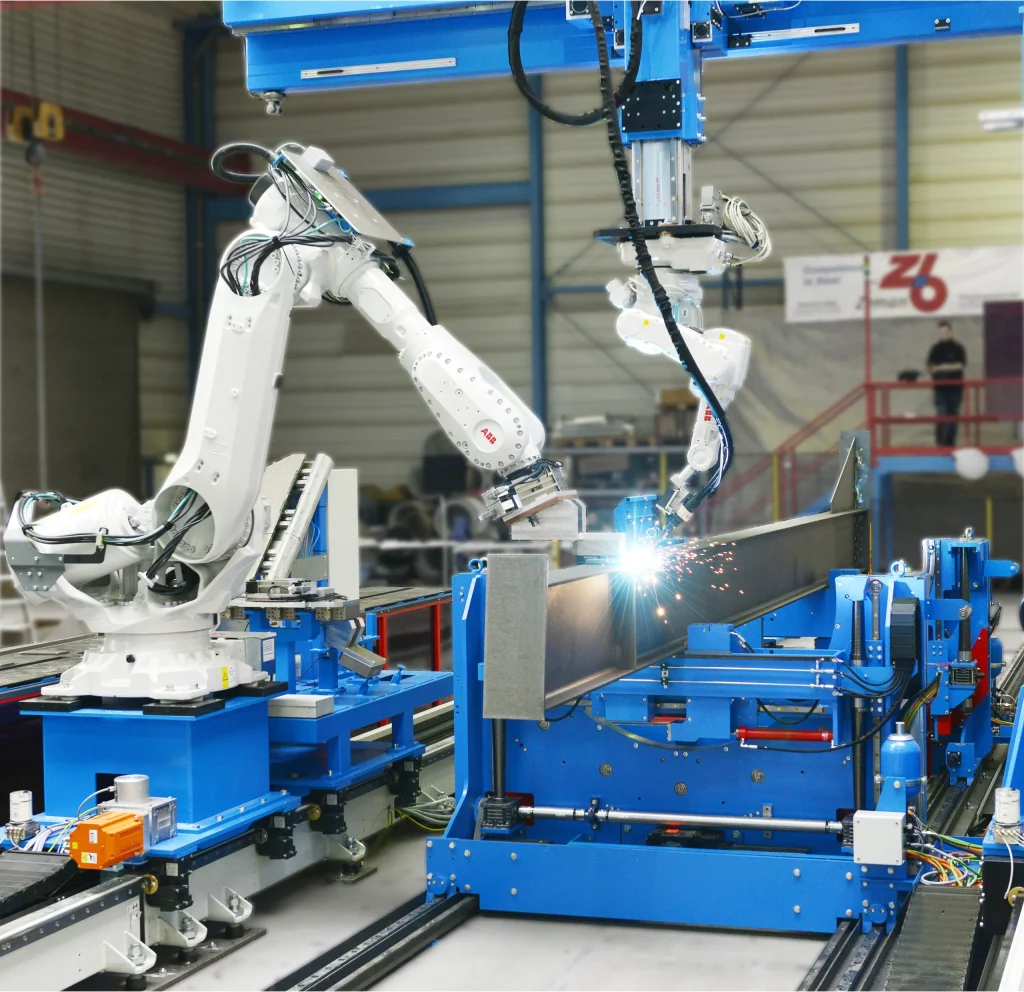
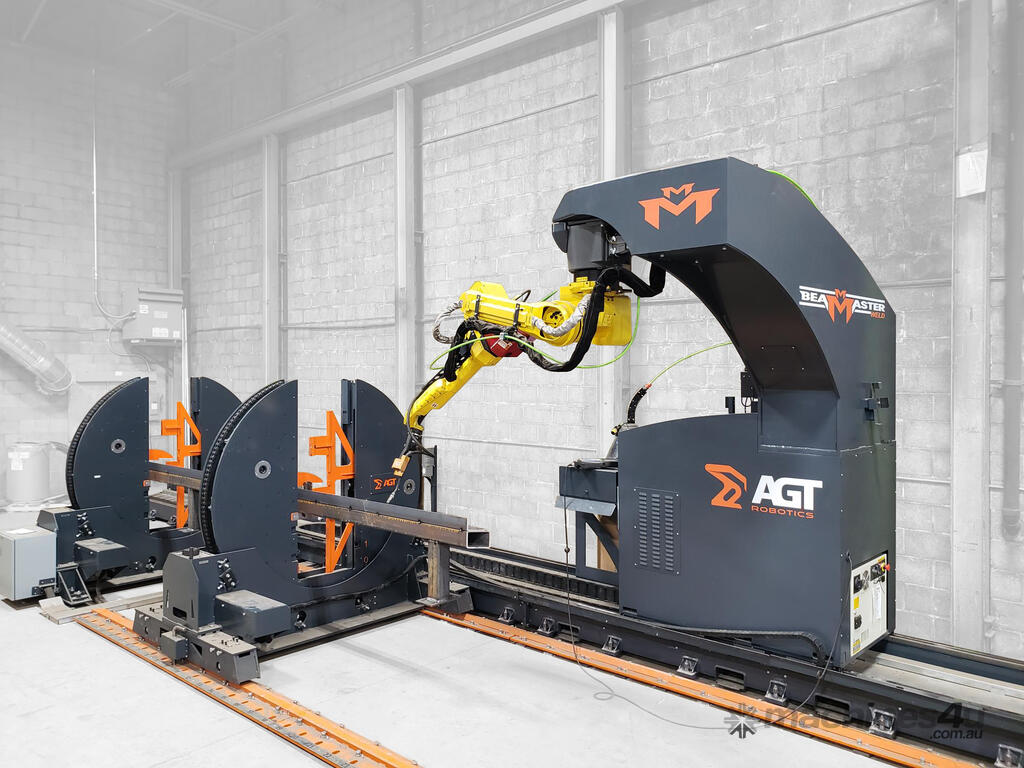
Manual Welders: Pros and Cons
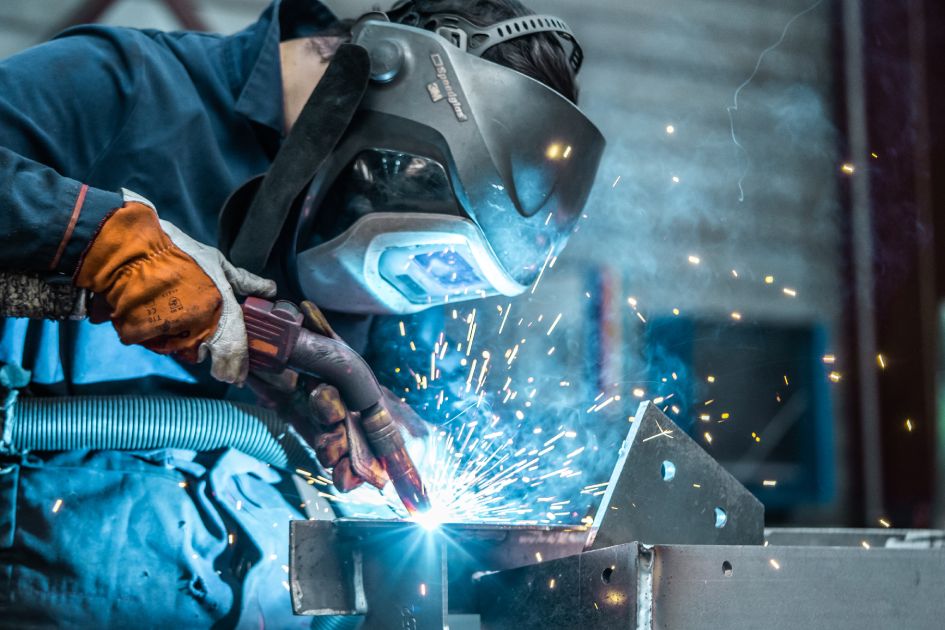
Manual welding, on the other hand, provides a level of flexibility that welding robots cannot match. Skilled welders can handle a wide variety of tasks, from large-scale projects to highly customized work. This adaptability makes manual welding particularly suitable for low-volume, bespoke fabrication. Furthermore, manual welders bring expertise to the table, able to make real-time adjustments when faced with challenges like material inconsistencies or complex joint angles. Their problem-solving ability ensures that unique or complicated projects are completed to a high standard.
Despite these advantages, manual welding has its downsides. Productivity is generally lower than that of welding robots, as human workers need breaks and are limited by fatigue. Besides, humans make errors so those can result in productivity losses: missing parts, parts that are not welded in the right locations, etc. However, this can be improved by implementing the scribing technology on the shop floor to minimize errors and facilitate the job on welding g stations. Moreover, manual welding introduces more variability in the quality of the welds, as human technique may fluctuate over time. Even experienced welders may face challenges in maintaining absolute consistency, particularly over long production runs. Safety is also a concern, as manual welding involves exposure to hazardous elements like high heat, sparks, and toxic fumes. Protective equipment helps, but the risks are still present, and the possibility of injury remains higher than in robotic welding environments.
Striking the Right Balance
For many steel fabrication businesses, a hybrid approach that combines both welding robots and manual welders may be the best solution: in a nutshell, humans for fitting and robots for welding is the approach that we recommend. This balance allows businesses to take advantage of the efficiency and precision of robotic systems, while still benefiting from the adaptability and problem-solving skills of manual welders.
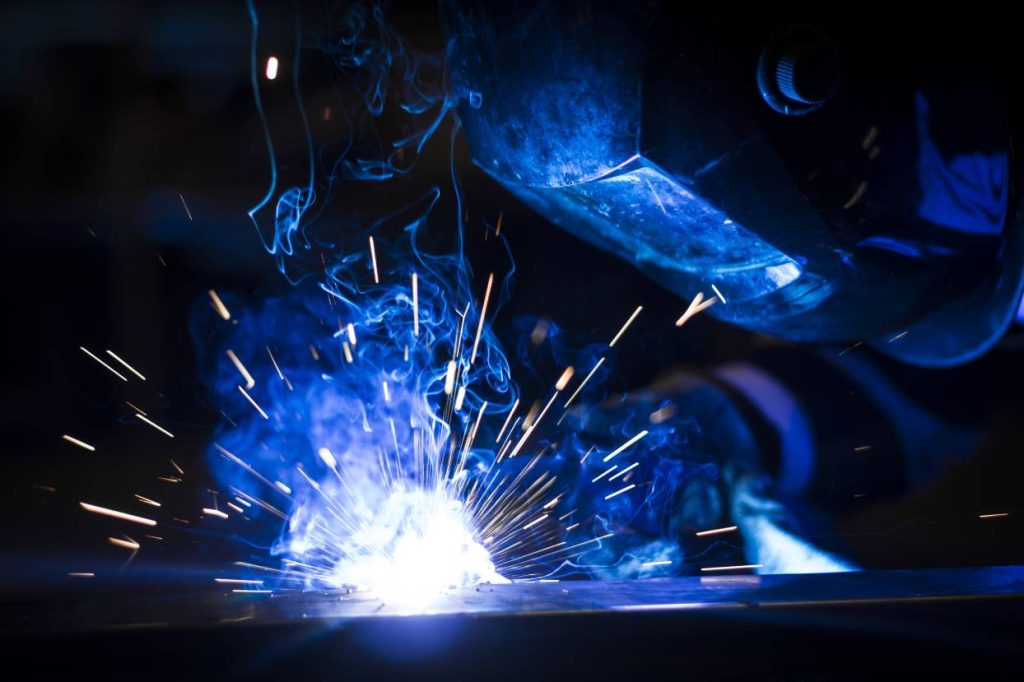
Besides, the decision between welding robots and manual welders depends on a company’s production needs, budget, and the complexity of the work involved. Companies that focus on large-scale production may find that robotic systems offer the greatest long-term benefits, while those that handle specialized projects might prefer the flexibility and craftsmanship of manual welding. In many cases, combining both methods strategically can yield the best results, maximizing both productivity and quality without sacrificing the advantages of either approach.
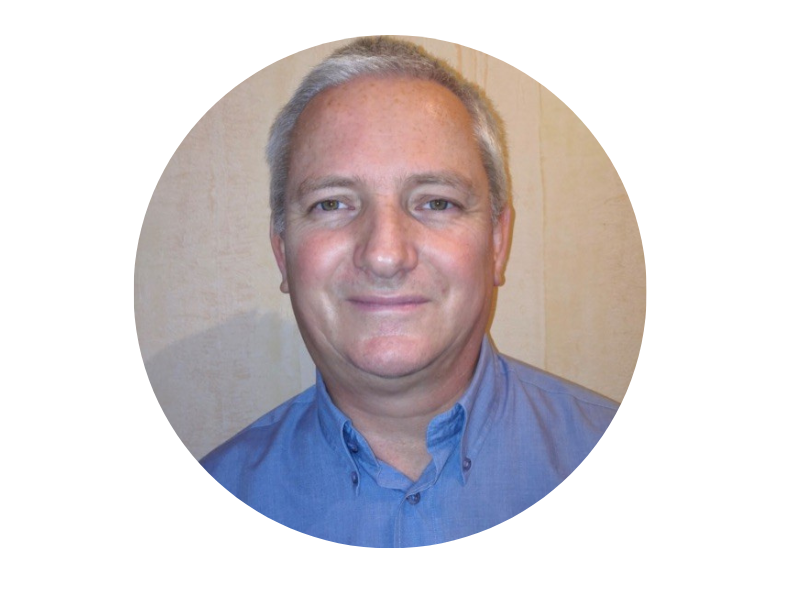
Would you like to go further?
Our experts are here to help you optimize your production.